"Mục sở thị" mô hình tăng trưởng xanh, phát triển bền vững tại các doanh nghiệp cao su
Các doanh nghiệp cao su thuộc Tập đoàn Công nghiệp Cao su Việt Nam đã tái chế bùn thải thành phân bón, sử dụng Biomass thay thế các loại khí đốt để sấy mủ… làm lợi hàng tỷ đồng, góp phần đưa chiến lược tăng trưởng xanh – phát triển bền vững đến những bước tiến mới.
Biến bùn thải thành phân bón
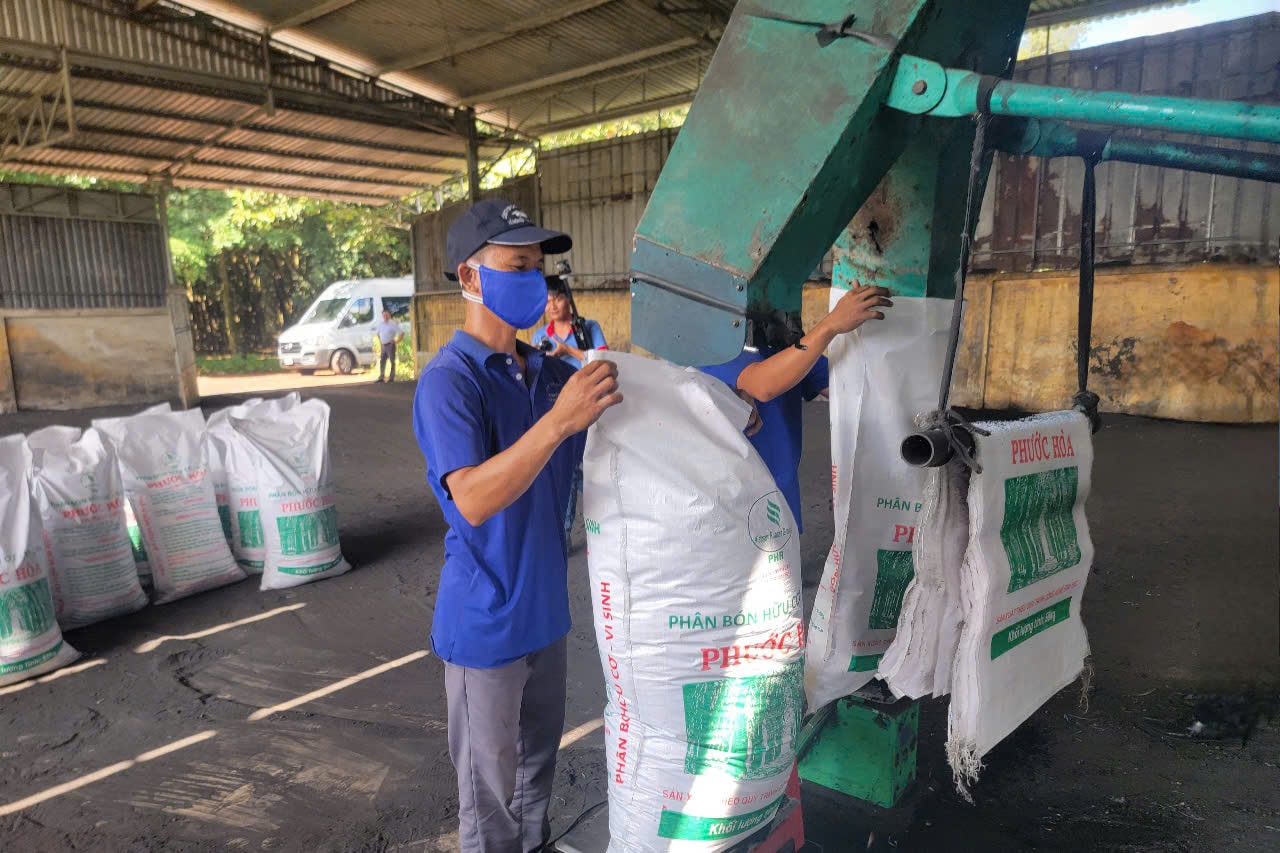
Tiếng máy động cơ của dây chuyền sản xuất phân bón tại Xưởng phân bón Phước Hòa (phường Chánh Phú Hòa, TP. Bến Cát cũ nay là phường Chánh Phú Hòa, TP. Hồ Chí Minh) thuộc Công ty Cổ phần Cao su Phước Hòa (Công ty Cao su Phước Hòa) chạy rầm rập trong nhà xưởng giữa không gian bao trùm là các rừng cao su bạt ngàn. Phía đầu dây chuyền, một công nhân lái máy xúc vận chuyển từng khối bùn (nguyên liệu để làm phân bón) đưa vào hệ thống dây chuyền.
Ở cuối dây chuyền, hai công nhân khác đang tất bật vận chuyển các bao phân thành phẩm và may miệng bao. Chỉ trong tích tắc từ nguyên liệu đầu vào là bùn thải đã biến thành hàng chục bao phân bón hữu cơ - vi sinh mang thương hiệu Phước Hòa.
Anh Lê Quốc Duy (phụ trách xưởng sản xuất phân bón) chia sẻ, hàng năm quá trình xử lý mủ cao su tồn đọng lại lượng bùn thải khá lớn, khoảng 10.000 tấn/năm. Trước thực tiễn đơn vị phải chi hàng tỷ đồng để thuê đơn vị khác xử lý lượng bùn thải này, từ năm 2015, đội ngũ cán bộ của công ty đã tiến hành nghiên cứu với mục tiêu biến bùn thải thành phân bón. Năm 2019, công trình đã được cơ quan chức năng cấp phép và đưa vào sản xuất với công suất 1.000 tấn phân bón/năm.
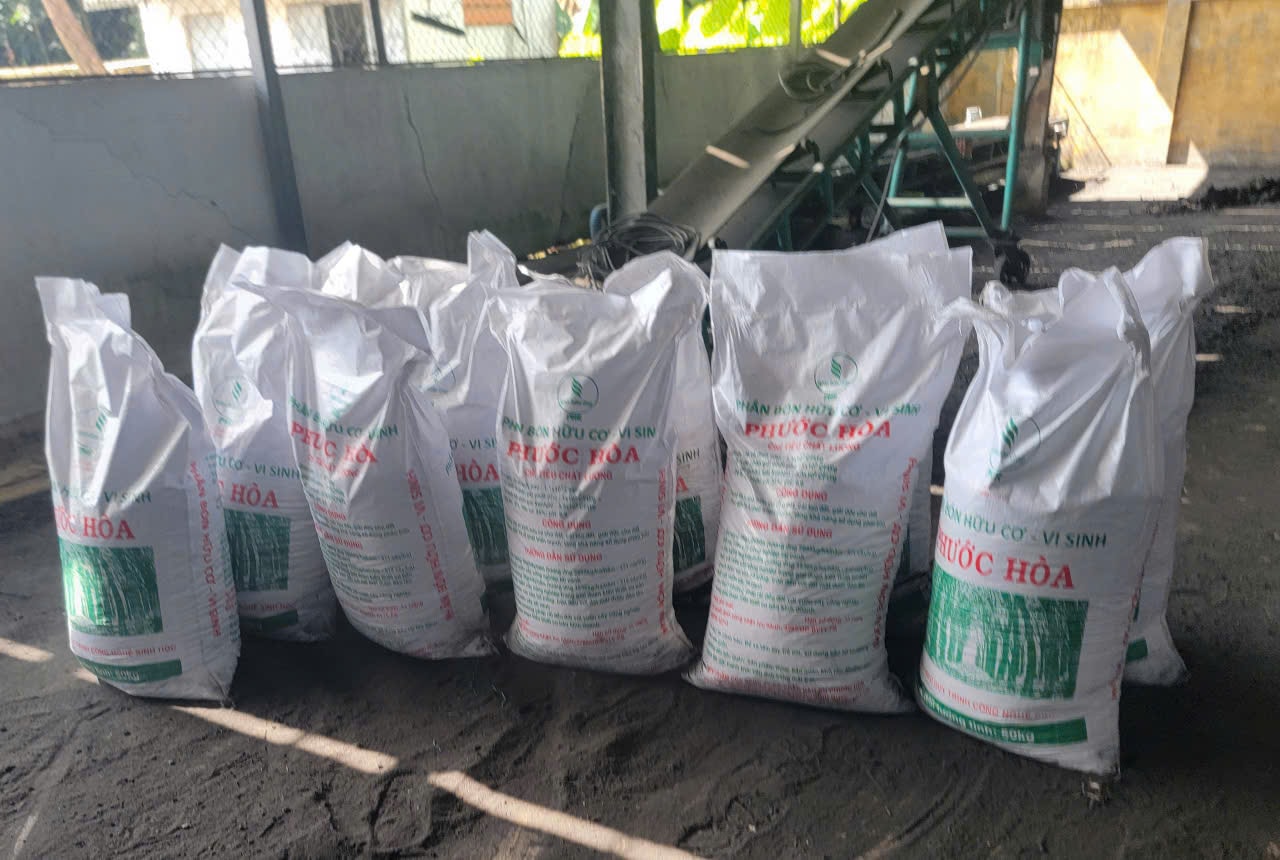
“Phân bón hữu cơ – vi sinh Phước Hòa được tái chế từ bùn thải qua quá trình ủ cùng các loại men vi sinh và trộn thêm các giá thể hữu cơ… hoàn toàn không sử dụng hóa chất. Công ty nhiều năm qua không tốn chi phí để thuê đơn vị xử lý bùn thải mà còn có khoảng 1.000 tấn phân bón/năm để bón cho các vườn cây. Giá phân bón do xưởng sản xuất khoảng 1,6 triệu đồng/tấn nhưng cũng loại phân hữu cơ này nếu mua ngoài thị trường thì phải ở giá hơn 2 triệu đồng/tấn. Công trình đã làm lợi cho công ty nhiều tỷ đồng/năm”, anh Duy cho hay.
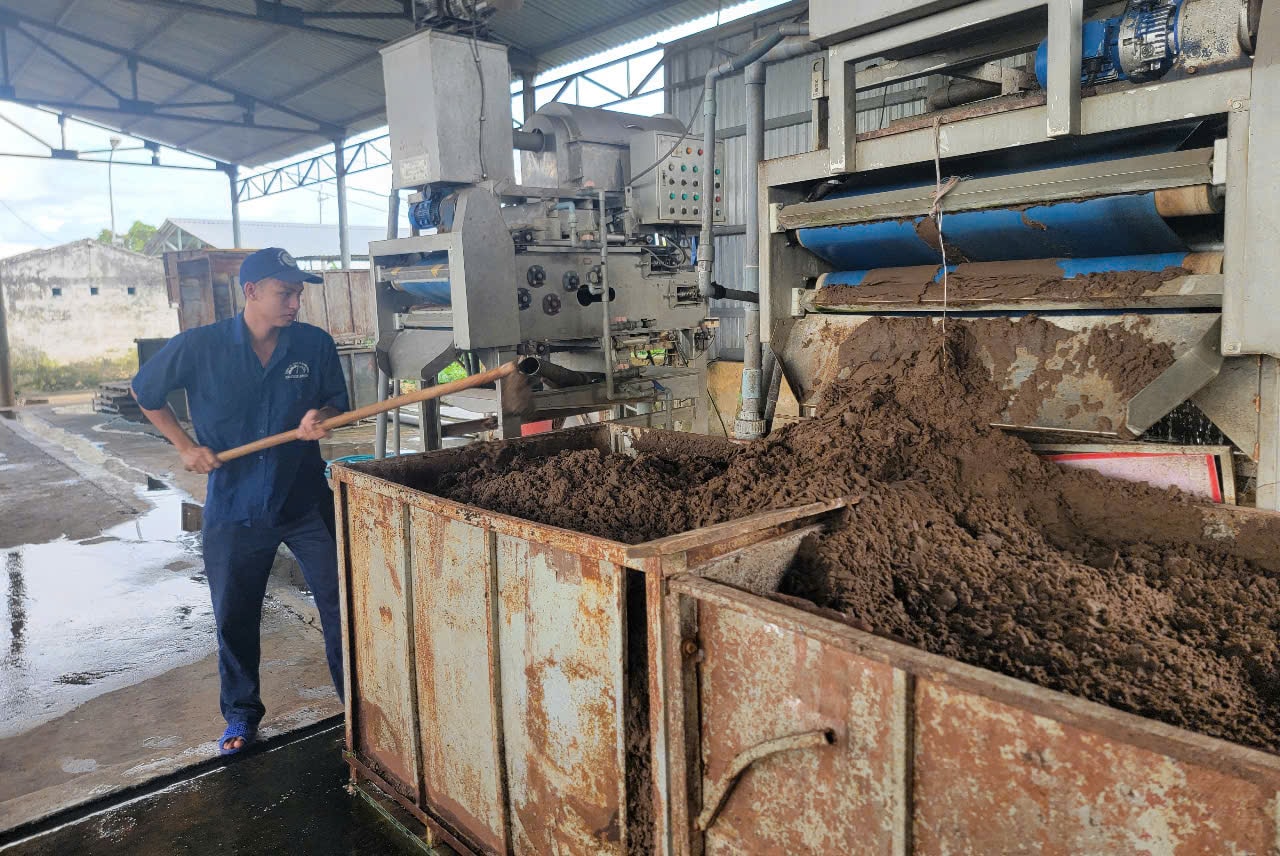
Cũng biến bùn thải thành phân bón để bón ngược lại cho cây cao su nhưng Công ty TNHH MTV Cao su Bình Long lại có “lối đi” khác. Đó là mô hình sử dụng bùn thải để nuôi trùn quế lấy phân bón.
Ông Bùi Đình Bảy, Phó tổng Giám đốc Công ty Cao su Bình Long cho biết bùn thải từ quá trình sản xuất mủ cao su được xử lý qua hệ thống, sau đó được đưa đến hệ thống máy ép. Từ năm 2021 đã tiến hành nghiên cứu đề tài trên và đến năm 2023 đưa vào vận hành chính thức. Mỗi năm hệ thống làm ra được khoảng 500 tấn phân trùn chỉ để bón lại cho cây cao su. Hiện tại Công ty có hai địa điểm nuôi trùn quế để lấy phân như thế này. Chất thải của các nhà máy thuộc Công ty mỗi năm khoảng 1.000 tấn và được sử dụng hết để nuôi trùn quế.
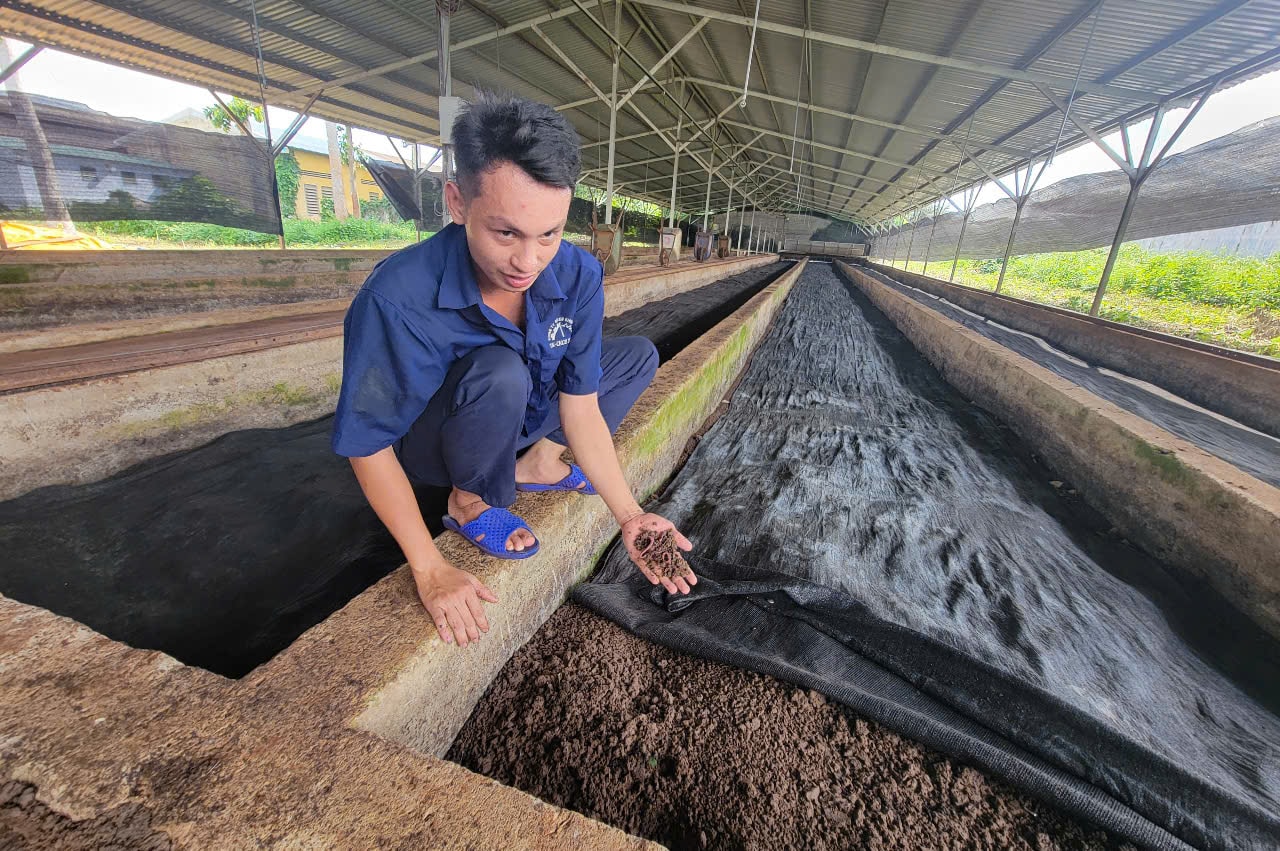
“Con trùn quế rất nhạy cảm với yếu tố môi trường nhưng nó đã ăn được bùn này và sinh trưởng thì điều này khẳng định môi trường tốt, chất bùn thải chúng tôi xử lý đạt chất lượng tốt. Tuy nhiên, để chất lượng phân tốt hơn, chúng tôi còn pha trộn phân bò với bùn thải để nuôi trùn tạo phân bón. Trước đây, Công ty phải tốn tiền để xử lý bùn thải nhưng hiện nay với công trình này chúng tôi không những không mất tiền xử lý bùn thải mà còn có phân trùn quế để bón lại cho cây cao su”, ông Bảy nói.
Sử dụng Biomass thay thế khí đốt để sấy mủ
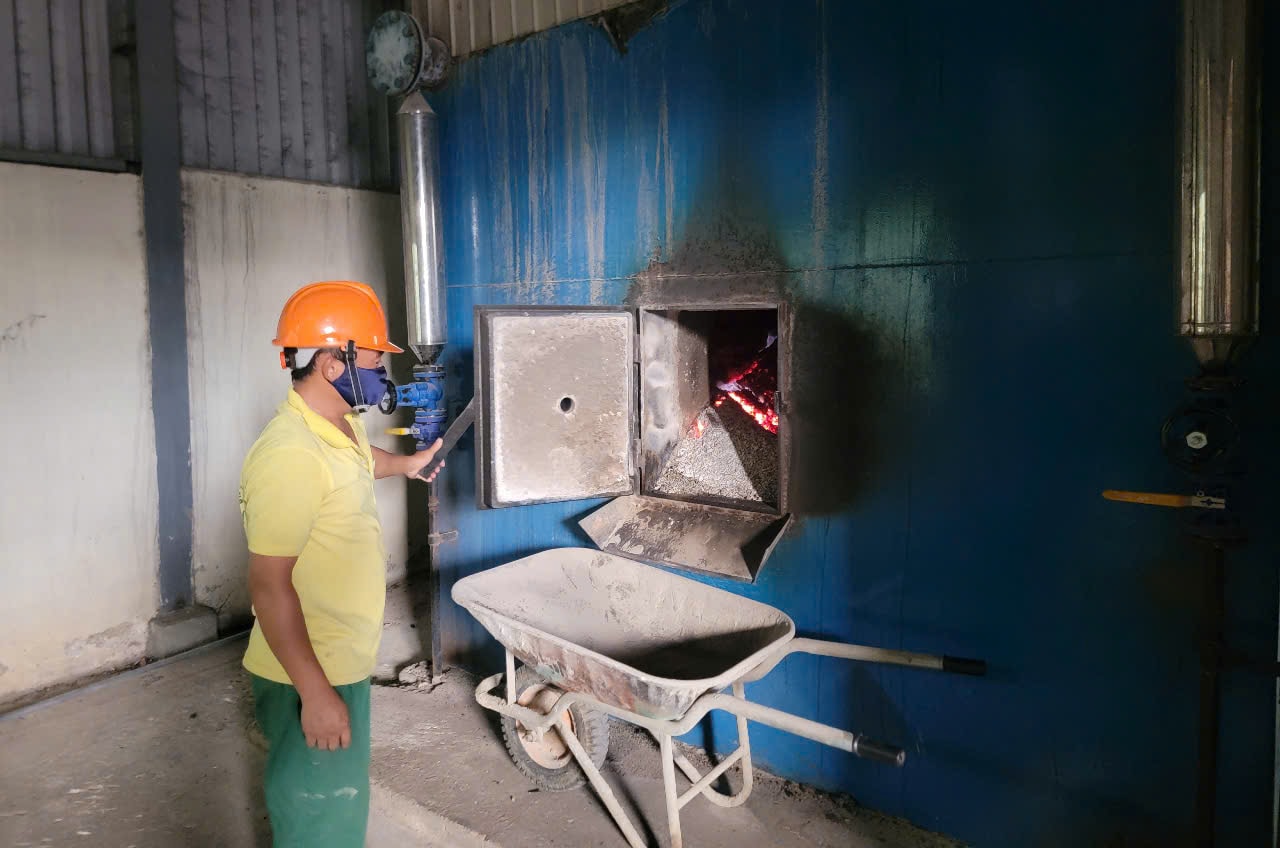
Một mô hình khác đang được nhiều doanh nghiệp của Tập đoàn Cao su như Công ty TNHH MTV Cao su Lộc Ninh (Công ty Cao su Lộc Ninh), Công ty TNHH MTV Cao su Phú Riềng (Công ty Cao su Phú Riềng)… vận hành nhiều năm nay trong quá trình sản xuất đó là mô hình sử dụng Biomass thay thế cho các loại khí đốt (dầu DO, gas…) để sấy mủ. Các doanh nghiệp đã sử dụng phế phẩm từ gỗ để làm chất đốt tạo hơi nóng trong quá trình sấy mủ cao su.
Tại khu vực lò đốt của Công ty Cao su Phú Riềng, hàng chục tấn dăm gỗ được tập kết để chuẩn bị đưa vào lò. Ông Lương Hồng Sắc, Trưởng phòng Quản lý chất lượng và Thị trường kinh doanh cho hay: Công ty chuyển đổi sấy mủ bằng gas sang mô hình Biomass từ năm 2020 đến nay. Ngoài vấn đề về chất lượng mủ khi sấy được nâng lên, việc sử dụng Biomass còn giúp tiết kiệm nhiều tỷ đồng/năm.
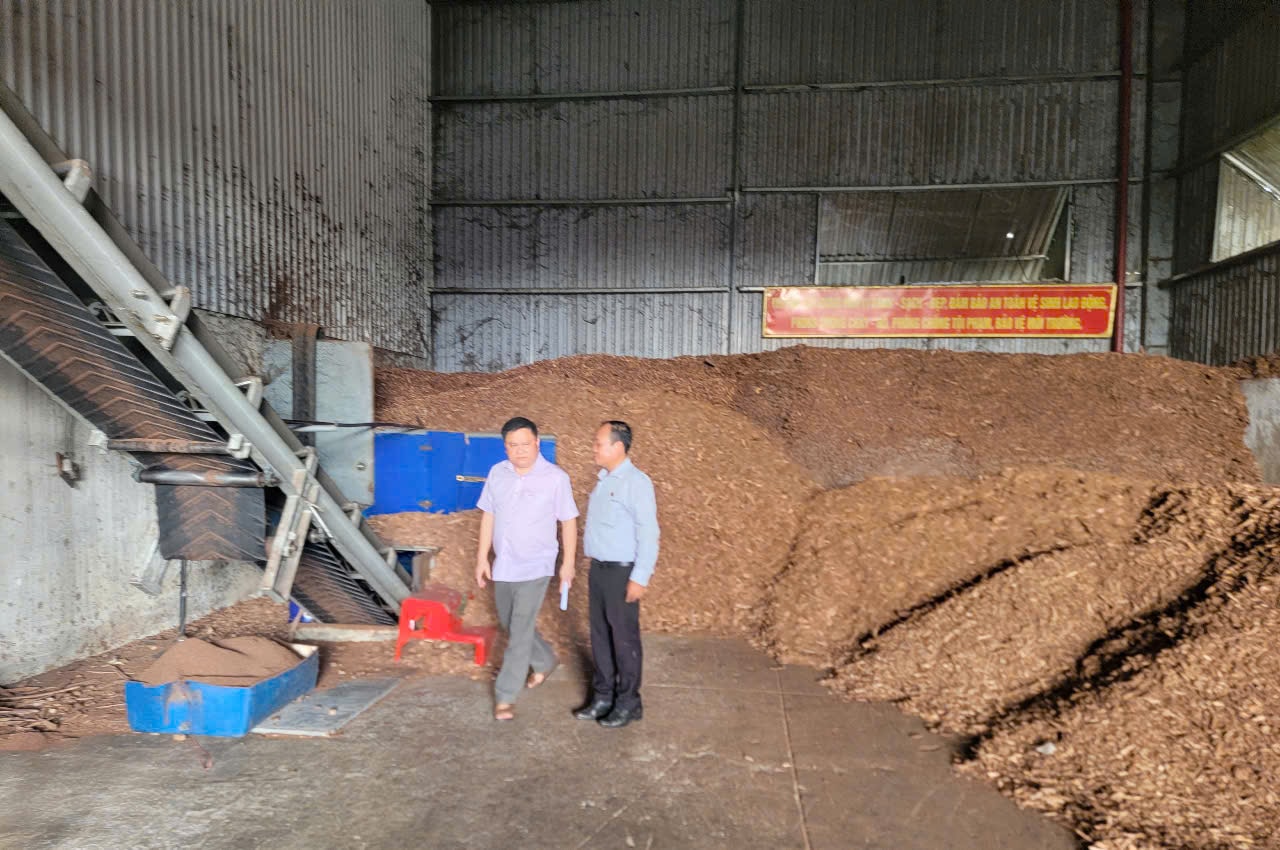
“Cụ thể: Có thời điểm để sấy 1 tấn mủ cao su thì tốn khoảng 440.000 đồng tiền gas nhưng nếu sấy bằng biomass chỉ 305.000 đồng/tấn mủ. Hàng năm sản lượng trung bình của công ty khoảng 30.000 tấn mủ và sử dụng khoảng 5.400 tấn dăm gỗ với chi phí khoảng 9 tỷ đồng nhưng nếu sử dụng gas để sấy sẽ tiêu tốn khoảng 12 – 13 tỷ đồng tiền gas. Như vậy mô hình Biomass đã tiết kiệm khoảng 4 tỷ đồng/năm. Ngoài ra, phế phẩm tro từ việc đốt lò còn được trộn với bùn thải, chế biến thành phân bón hữu cơ bón lại cho cây cao su”, ông Sắc cho hay.
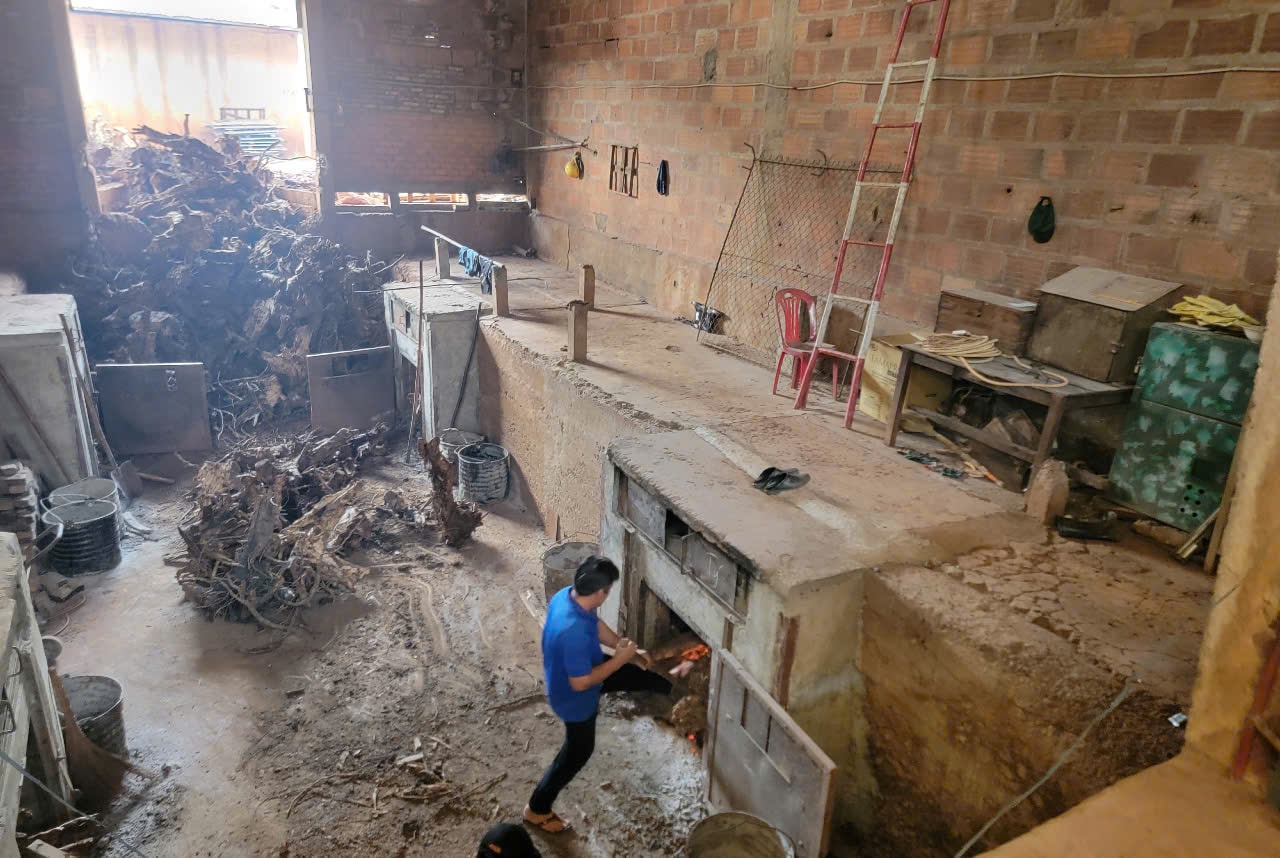
Trong khi đó, hàng ngày những người công nhân làm công việc đốt lò tại lò đốt sấy mủ của Công ty Cao su Lộc Ninh luôn túc trực sẵn để vận chuyển các gốc cao su thanh lý vào miệng lò. Lò đốt sấy mủ của Công ty Cao su Lộc Ninh có tuổi đời lâu nhất, hiện đã trăm năm tuổi nhưng hàng ngày vẫn đỏ lửa để sấy mủ cao su. Các tấm mủ cao su được đưa vào lò và sấy bằng hơi nóng từ củi trong thời gian khoảng 7 ngày.
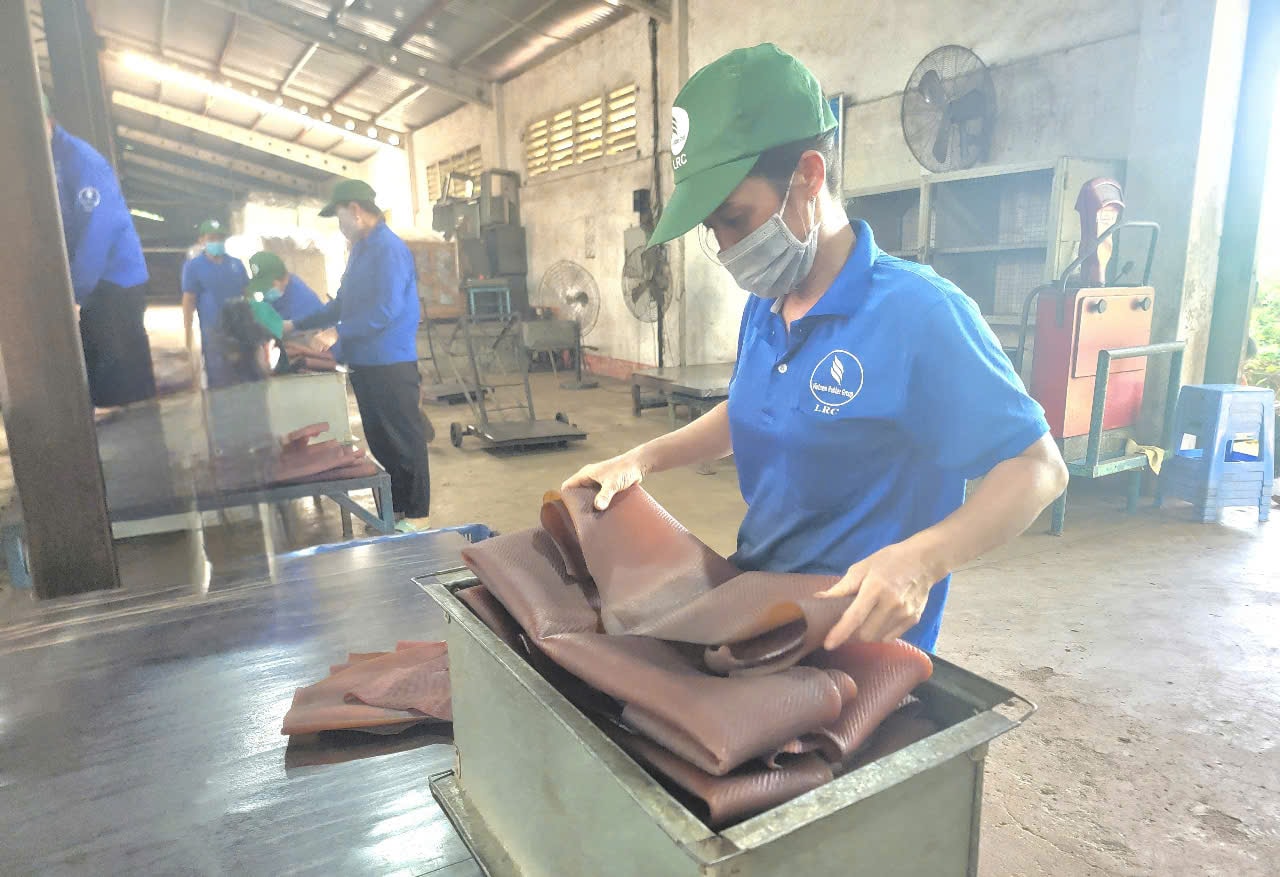
Đứng quan sát các công nhân đốt lò, ông Nguyễn Trường Giang – Phó tổng Giám đốc Công ty Cao su Lộc Ninh chia sẻ, nhà máy sấy này được người Pháp xây dựng từ năm 1909 và được giữ nguyên trạng cho đến giờ. Các sản phẩm cao su được sấy từ lò này phần lớn xuất sang các nước châu Âu và rất hút hàng bởi màu mủ được sấy từ lò đốt này là màu mủ đẹp nhất và chất lượng rất tốt.
“Nguyên liệu để đốt lò phần lớn là gốc cao su thanh lý. Tro từ việc đốt lò là một “đặc sản” để hòa lẫn với đất hoặc bùn thải (đã tái chế) để bón lại cho cây cao su. Chúng tôi dùng chính tro này để bón lại cho cây cao su, cây phát triển và cho mủ với chất lượng cao”, ông Giang nói.